- No elements found. Consider changing the search query.
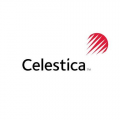
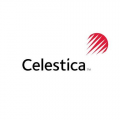
ทักษะ:
Automation, Assembly, Data Entry
ประเภทงาน:
งานประจำ
เงินเดือน:
สามารถต่อรองได้
- Under supervision, assist in the development and implementation of new standard automation solutions and/or "off the shelf" equipment. Support the equipment's software and hardware upgrades and qualification.
- Support the hardware and software improvements of both Celestica led developments and off the shelf equipment via the analysis of Overall Equipment Efficiency (OEE) and other available data,.
- Support manufacturing operations to program, qualify, deploy, optimize and maintain ...
- Execute maintenance activities with supervision.
- Support customer product road map using Celestica Automation E2E process and tools such as User Requirement Specifications (URS) and Design for Automation Assembly (DFAA).
- Knowledge/Skills/Competencies.
- Refer to technical skills below.
- Physical Demands.
- Duties of this position are performed in a normal office environment.
- Duties may require extended periods of sitting and sustained visual concentration on a computer monitor or on numbers and other detailed data.
- Repetitive manual movements (e.g., data entry, using a computer mouse, using a calculator, etc.) are frequently required.
- Occasional travel may be required.
- Typical Experience.
- Entry level to 1 year.
- Typical Education.
- Bachelor degree or consideration of an equivalent combination of education and experience.
- Educational Requirements may vary by Geography.
- Notes.
- This job description is not intended to be an exhaustive list of all duties and responsibilities of the position. Employees are held accountable for all duties of the job. Job duties and the % of time identified for any function are subject to change at any time.
- Celestica is an equal opportunity employer. All qualified applicants will receive consideration for employment and will not be discriminated against on any protected status (including race, religion, national origin, gender, sexual orientation, age, marital status, veteran or disability status or other characteristics protected by law).
- At Celestica we are committed to fostering an inclusive, accessible environment, where all employees and customers feel valued, respected and supported. Special arrangements can be made for candidates who need it throughout the hiring process. Please indicate your needs and we will work with you to meet them.
- Celestica (NYSE, TSX: CLS) enables the world s best brands. Through our recognized customer-centric approach, we partner with leading companies in Aerospace and Defense, Communications, Enterprise, HealthTech, Industrial, Capital Equipment and Energy to deliver solutions for their most complex challenges. As a leader in design, manufacturing, hardware platform and supply chain solutions, Celestica brings global expertise and insight at every stage of product development - from drawing board to full-scale production and after-market services for products from advanced medical devices, to highly engineered aviation systems, to next-generation hardware platform solutions for the Cloud. Headquartered in Toronto, with talented teams spanning 40+ locations in 13 countries across the Americas, Europe and Asia, we imagine, develop and deliver a better future with our customers.
- Celestica would like to thank all applicants, however, only qualified applicants will be contacted.
- Celestica does not accept unsolicited resumes from recruitment agencies or fee based recruitment services.
ประสบการณ์:
1 ปีขึ้นไป
ทักษะ:
CAD, SOLIDWORKS, Assembly
ประเภทงาน:
งานประจำ
เงินเดือน:
สามารถต่อรองได้
- Design mechanical parts and assemblies, focusing on sheet metal components and jigs/fixtures.
- Create detailed 3D models and 2D drawings using CAD software (e.g., SolidWorks, CATIA, NX, or equivalent).
- Collaborate with Engineering, manufacturing, and process engineers to ensure designs are practical and cost-effective.
- Support the prototyping, assembly, testing, and validation of new designs.
- Modify and improve existing designs based on feedback and performance data.
- Maintain accurate documentation and follow engineering change processes.
- Knowledge/Skills/Competencies.
- Bachelor s degree in Mechanical Engineering or a related field..
- Minimum of 1 year of experience in mechanical design, particularly with sheet metal and fixture design..
- Proficiency in 3D CAD tools (SolidWorks preferred)..
- Strong understanding of GD&T, manufacturing processes, and material selection..
- Experience with DFM/DFA principles..
- Good communication skills and ability to work in cross-functional teams..
- Typical Experience.
- New graduates with strong academic or internship experience are encouraged to apply.
- Typical Education.
- Bachelor s degree in Mechanical Engineering or a related field..
- Notes.
- This job description is not intended to be an exhaustive list of all duties and responsibilities of the position. Employees are held accountable for all duties of the job. Job duties and the % of time identified for any function are subject to change at any time.
- Celestica is an equal opportunity employer. All qualified applicants will receive consideration for employment and will not be discriminated against on any protected status (including race, religion, national origin, gender, sexual orientation, age, marital status, veteran or disability status or other characteristics protected by law).
- At Celestica we are committed to fostering an inclusive, accessible environment, where all employees and customers feel valued, respected and supported. Special arrangements can be made for candidates who need it throughout the hiring process. Please indicate your needs and we will work with you to meet them.
- Celestica (NYSE, TSX: CLS) enables the world s best brands. Through our recognized customer-centric approach, we partner with leading companies in Aerospace and Defense, Communications, Enterprise, HealthTech, Industrial, Capital Equipment and Energy to deliver solutions for their most complex challenges. As a leader in design, manufacturing, hardware platform and supply chain solutions, Celestica brings global expertise and insight at every stage of product development - from drawing board to full-scale production and after-market services for products from advanced medical devices, to highly engineered aviation systems, to next-generation hardware platform solutions for the Cloud. Headquartered in Toronto, with talented teams spanning 40+ locations in 13 countries across the Americas, Europe and Asia, we imagine, develop and deliver a better future with our customers.
- Celestica would like to thank all applicants, however, only qualified applicants will be contacted.
- Celestica does not accept unsolicited resumes from recruitment agencies or fee based recruitment services.
ประสบการณ์:
5 ปีขึ้นไป
ทักษะ:
Electronics, Assembly
ประเภทงาน:
งานประจำ
เงินเดือน:
สามารถต่อรองได้
- Be responsible for DB, WB, Alignment, test equipment setup, buyoff, repairing and maintenance.
- Reporting to Equipment & Maintenance engineer to drive equipment technical problem resolution.
- Perform equipment PM, Equipment Calibration.
- Installation, modification, upgrade manufacturing equipment.
- Improve equipment performance and reliability.
- Reduce equipment downtime.
- Onsite trouble shooting and repairing when equipment down.
- Required Qualification Associate Degree of Engineering or above in optical Fiber communication, electrical, electronics, computer or related field.
- Minimum 5 years of experience as equipment/process technician in semiconductor assembly or optical products.
- Experience must related with die attach, wire bonding, mechanical alignment and test. MRSI, Datacon, ASM Amicra, 4T die bonder, KNS, ASM wire bonder is preferred.
- Can accept day and night shift rotating working in cleaning room.
- Working with team and under pressure of some situation.
- Machine Preventive Maintenance Utilize preventive maintenance and resolve technical issue of operation machines to reduce downtime and/or break down of production processes.
- Experienced for alignment process and optical test process.
- Equipment of alignment and test module.
- We are an equal opportunity employer and value diversity at our company. We do not discriminate on the basis of race, religion, color, national origin, sex, gender, gender expression, sexual orientation, age, marital status, veteran status, or disability status. We will ensure that individuals with disabilities are provided reasonable accommodation to participate in the job application or interview process, to perform essential job functions, and to receive other benefits and privileges of employment. Please contact us to request accommodation.
ประสบการณ์:
6 ปีขึ้นไป
ทักษะ:
Assembly
ประเภทงาน:
งานประจำ
เงินเดือน:
สามารถต่อรองได้
- Administers, organizes and conducts training in the assembly, inspection, testing and repair of company products.
- Develops and delivers training packages for production equipment.
- Trains and certifies production operators in adding, removing and replacing component parts including through-hole and surface mount component technology.
- Trains in areas relative to the assembly, modification, repair and standards associated with company products etc.
- Provides on-the-job training for operation of production equipment.
- Designs training curriculum and courses to prepare employees for production positions, (can include third party training providers).
- Tests employees and audits trained operators.
- Certifies or decertifies operators as a result of testing.
- Maintains a training database for all skills related training for direct staff and ESD/technical certification for other staff.
- Disseminates re-certification notices, creates and distributes certification cards, and updates employees training records.
- Knowledge/Skills/Competencies.
- In-depth knowledge of technologies, including: through-hole, surface mount, surface mount fine/extra fine pitch, and associated modification and repair techniques.
- IPC Class A Instructor Certification.
- Ability to train trainers.
- Proficient in computer applications including Windows NT, Lotus Notes, MS Office Suite, etc.
- Strong presentation, teaching and coaching skills.
- Ability to communicate effectively, both verbally and in writing, to a diverse group of internal customers.
- Ability to communicate effectively, both in one to one and group situations.
- Physical Demands.
- Duties of this position are performed in a manufacturing environment with occasional exposure to elements such as noise, dust, chemicals, operating machinery, temperature extremes, etc.
- Duties of this position may occasionally require light physical effort and exertion such as prolonged repetitive motion requiring manual dexterity and precise hand/eye co-ordination, standing, sitting and or standing in a confined work station, climbing using equipment, handling lightweight materials, etc.
- Duties of this position may occasionally require heavy manual effort and considerable exertion for short periods including lifting objects.
- Duties often require extended periods of sustained visual concentration on detailed documentation and product assemblies.
- Above demands are carried out within the local existing Health and Safety guidelines.
- Typical Experience.
- Four to six years of relevant experience.
- Typical Education.
- Two or three year community college diploma in a related field, or consideration of an equivalent combination of education and experience.
- Educational Requirements may vary by Geography.
- Notes.
- This job description is not intended to be an exhaustive list of all duties and responsibilities of the position. Employees are held accountable for all duties of the job. Job duties and the % of time identified for any function are subject to change at any time.
- Celestica is an equal opportunity employer. All qualified applicants will receive consideration for employment and will not be discriminated against on any protected status (including race, religion, national origin, gender, sexual orientation, age, marital status, veteran or disability status or other characteristics protected by law).
- At Celestica we are committed to fostering an inclusive, accessible environment, where all employees and customers feel valued, respected and supported. Special arrangements can be made for candidates who need it throughout the hiring process. Please indicate your needs and we will work with you to meet them.
- Celestica (NYSE, TSX: CLS) enables the world s best brands. Through our recognized customer-centric approach, we partner with leading companies in Aerospace and Defense, Communications, Enterprise, HealthTech, Industrial, Capital Equipment and Energy to deliver solutions for their most complex challenges. As a leader in design, manufacturing, hardware platform and supply chain solutions, Celestica brings global expertise and insight at every stage of product development - from drawing board to full-scale production and after-market services for products from advanced medical devices, to highly engineered aviation systems, to next-generation hardware platform solutions for the Cloud. Headquartered in Toronto, with talented teams spanning 40+ locations in 13 countries across the Americas, Europe and Asia, we imagine, develop and deliver a better future with our customers.
- Celestica would like to thank all applicants, however, only qualified applicants will be contacted.
- Celestica does not accept unsolicited resumes from recruitment agencies or fee based recruitment services.
ประสบการณ์:
2 ปีขึ้นไป
ทักษะ:
Assembly, Electronics
ประเภทงาน:
งานประจำ
เงินเดือน:
สามารถต่อรองได้
- Reads and analyzes schematic diagrams, circuit descriptions and similar technical information.
- Troubleshoots and repairs failed products. Inspects for physical and visual quality requirements.
- Isolates and replaces faulty components.
- Sets up, operates, and adjusts test sets and auxiliary equipment.
- Proves tests and test sets.
- Troubleshoots and repairs test equipment/fixture problems.
- Performs reactive maintenance on electromechanical surface mount assembly equipment.
- Provides basic product technical data setup support for printed circuit boards, subassemblies, or other related company products.
- Reads and analyzes schematic diagrams, Bills of Materials, Component Data, Engineering Change Order and similar technical information.
- Inspects for standard quality requirements.
- Maintains records for technical product data availability, data integrity, and data completeness.
- Schedules and performs preventative maintenance.
- Maintains records for equipment availability, failure analysis and maintenance.
- Maintains equipment spare parts database.
- Tracks spare parts usage and maintains inventory of equipment spare parts.
- Helps move, install, set up and refurbish equipment.
- Knowledge/Skills/Competencies.
- Engineering Foundation Competencies.
- Knowledge of mechanical design methods, procedures and processes.
- Knowledge of and ability to use MCAD systems.
- Knowledge of SMT placement equipment, specifications and operation.
- Basic knowledge of computer programming.
- Knowledge of tooling design and vendor fabrication of mechanical assemblies.
- Strong math skills.
- Ability to manipulate textual data, edit files and use E-Mail with HP-UX tools.
- Ability to compile data, compute quantities, determine materials needed, and prepare cost estimates.
- Knowledge of quality standards.
- Ability to effectively communicate with a variety of internal customers.
- Knowledge of electrical, electromechanical and pneumatic systems and principals of operation.
- Knowledge of production operations and operator responsibilities.
- Ability to analyze equipment and systems, troubleshoot problems and make appropriate repairs.
- Knowledge of digital electronics and repair methodologies.
- Knowledge of personal computers and Windows applications.
- Knowledge of quality standards.
- Ability to effectively communicate with a variety of internal customers.
- Physical Demands.
- Duties of the position are performed in a manufacturing environment with frequent exposure to noise, dust, chemicals, operating machinery, temperature extremes, hazardous substances, etc.
- Duties require extended periods of sustained visual concentration on detailed documentation and product assemblies.
- Duties of the position require periodic light physical effort and exertion including prolonged repetitive motions, sitting in confined workspaces, using tools and equipment, and moving and handling materials.
- Duties may require periodic heavy manual effort including lifting objects over 20 pounds.
- Typical Experience.
- Zero to two years of relevant experience.
- Typical Education.
- Two or three year community college diploma in a related field, or an equivalent combination of education and experience.
- Educational requirements may vary by geography.
- Notes.
- This job description is not intended to be an exhaustive list of all duties and responsibilities of the position. Employees are held accountable for all duties of the job. Job duties and the % of time identified for any function are subject to change at any time.
- Celestica is an equal opportunity employer. All qualified applicants will receive consideration for employment and will not be discriminated against on any protected status (including race, religion, national origin, gender, sexual orientation, age, marital status, veteran or disability status or other characteristics protected by law).
- At Celestica we are committed to fostering an inclusive, accessible environment, where all employees and customers feel valued, respected and supported. Special arrangements can be made for candidates who need it throughout the hiring process. Please indicate your needs and we will work with you to meet them.
- Celestica (NYSE, TSX: CLS) enables the world s best brands. Through our recognized customer-centric approach, we partner with leading companies in Aerospace and Defense, Communications, Enterprise, HealthTech, Industrial, Capital Equipment and Energy to deliver solutions for their most complex challenges. As a leader in design, manufacturing, hardware platform and supply chain solutions, Celestica brings global expertise and insight at every stage of product development - from drawing board to full-scale production and after-market services for products from advanced medical devices, to highly engineered aviation systems, to next-generation hardware platform solutions for the Cloud. Headquartered in Toronto, with talented teams spanning 40+ locations in 13 countries across the Americas, Europe and Asia, we imagine, develop and deliver a better future with our customers.
- Celestica would like to thank all applicants, however, only qualified applicants will be contacted.
- Celestica does not accept unsolicited resumes from recruitment agencies or fee based recruitment services.
ประสบการณ์:
3 ปีขึ้นไป
ทักษะ:
Purchasing, Automation, Assembly
ประเภทงาน:
งานประจำ
เงินเดือน:
สามารถต่อรองได้
- With minimal oversight, execute tasks in the equipment development project including the purchasing and implementation of standard off the shelf solutions and/or development of new standard automation equipment solutions.
- Execute the hardware and software improvements of automated lines and off the shelf equipment, via the analysis of Overall Equipment Efficiency (OEE) and other available data.
- Liaise with multiple stakeholders including solution providers for design, technical ...
- Support correcting of technical problems impacting equipment validation activities associated with Factory Acceptance Test (FAT) and Site Acceptance Test (SAT).
- Execute and optimize/improve maintenance plans and activities.
- Support customer product road map using Celestica Automation E2E process and tools such as User Requirement Specifications (URS) and Design for Automation Assembly (DFAA) and PM workbook.
- Drive problem solving and corrective actions related to causes of machine failures, speed loss or quality issues.
- Work with Process Engineering to ensure equipment is statistically capable of meeting the product manufacturing requirements.
- Knowledge/Skills/Competencies.
- Refer to technical skills below.
- Physical Demands.
- Duties of this position are performed in a normal office environment.
- Duties may require extended periods of sitting and sustained visual concentration on a computer monitor or on numbers and other detailed data.
- Repetitive manual movements (e.g., data entry, using a computer mouse, using a calculator, etc.) are frequently required.
- Occasional travel may be required.
- Typical Experience.
- 1 to 3 years of related experienc;Experience in similar job roles.
- Typical Education.
- Bachelor degree or consideration of an equivalent combination of education and experience.
- Educational Requirements may vary by Geography.
- Notes.
- This job description is not intended to be an exhaustive list of all duties and responsibilities of the position. Employees are held accountable for all duties of the job. Job duties and the % of time identified for any function are subject to change at any time.
- Celestica is an equal opportunity employer. All qualified applicants will receive consideration for employment and will not be discriminated against on any protected status (including race, religion, national origin, gender, sexual orientation, age, marital status, veteran or disability status or other characteristics protected by law).
- At Celestica we are committed to fostering an inclusive, accessible environment, where all employees and customers feel valued, respected and supported. Special arrangements can be made for candidates who need it throughout the hiring process. Please indicate your needs and we will work with you to meet them.
- Celestica (NYSE, TSX: CLS) enables the world s best brands. Through our recognized customer-centric approach, we partner with leading companies in Aerospace and Defense, Communications, Enterprise, HealthTech, Industrial, Capital Equipment and Energy to deliver solutions for their most complex challenges. As a leader in design, manufacturing, hardware platform and supply chain solutions, Celestica brings global expertise and insight at every stage of product development - from drawing board to full-scale production and after-market services for products from advanced medical devices, to highly engineered aviation systems, to next-generation hardware platform solutions for the Cloud. Headquartered in Toronto, with talented teams spanning 40+ locations in 13 countries across the Americas, Europe and Asia, we imagine, develop and deliver a better future with our customers.
- Celestica would like to thank all applicants, however, only qualified applicants will be contacted.
- Celestica does not accept unsolicited resumes from recruitment agencies or fee based recruitment services.
ทักษะ:
Assembly, English
ประเภทงาน:
งานประจำ
เงินเดือน:
สามารถต่อรองได้
- New product leader and co-ordinate..
- Communicate to customer for EC related issue and NPI activities..
- Co-ordinate with concern team to meet the customer product's requirements..
- Co-ordinate with concern team to Process BOM release in Matrix system..
- Generate ECN history of Optical Module and PCBA for traceability..
- Assign indirect mat'l and maintain indirect mat'l AVL..
- Process Change Management system..
- Manage the shop floor BOM for support production build..
- Cost reduction..
- Knowledge/Skills/Competencies.
- Refer to technical skills below.
- Typical Experience.
- Optical Components process assembly, splicing, die attach, alignment or PCBA process assembly experience in SMT, wave soldering and mechanical assembly..
- Knowledge in NPI, new product, new process, BOM.
- Good leadership and self-motivation.
- Good in English and communicate well..
- Typical Education.
- Bachelor or higher in Electronics or Mechanical Engineering or equivalent.
- Notes.
- This job description is not intended to be an exhaustive list of all duties and responsibilities of the position. Employees are held accountable for all duties of the job. Job duties and the % of time identified for any function are subject to change at any time.
- Celestica is an equal opportunity employer. All qualified applicants will receive consideration for employment and will not be discriminated against on any protected status (including race, religion, national origin, gender, sexual orientation, age, marital status, veteran or disability status or other characteristics protected by law).
- At Celestica we are committed to fostering an inclusive, accessible environment, where all employees and customers feel valued, respected and supported. Special arrangements can be made for candidates who need it throughout the hiring process. Please indicate your needs and we will work with you to meet them.
- Celestica (NYSE, TSX: CLS) enables the world s best brands. Through our recognized customer-centric approach, we partner with leading companies in Aerospace and Defense, Communications, Enterprise, HealthTech, Industrial, Capital Equipment and Energy to deliver solutions for their most complex challenges. As a leader in design, manufacturing, hardware platform and supply chain solutions, Celestica brings global expertise and insight at every stage of product development - from drawing board to full-scale production and after-market services for products from advanced medical devices, to highly engineered aviation systems, to next-generation hardware platform solutions for the Cloud. Headquartered in Toronto, with talented teams spanning 40+ locations in 13 countries across the Americas, Europe and Asia, we imagine, develop and deliver a better future with our customers.
- Celestica would like to thank all applicants, however, only qualified applicants will be contacted.
- Celestica does not accept unsolicited resumes from recruitment agencies or fee based recruitment services.
ประสบการณ์:
8 ปีขึ้นไป
ทักษะ:
Assembly, GIS, Instrument, English
ประเภทงาน:
งานประจำ
เงินเดือน:
สามารถต่อรองได้
- Assist the project manager with all technical aspects and documentation.
- Control and evaluate project progress, reporting on time and quality.
- Coordinate activities of suppliers and subcontractors.
- Perform quality checks and inspections to ensure assembly work meets requirements.
- Generate reports, perform NCC-reporting, and ensure corrective/preventive actions.
- Organize, compile, submit, and control technical documents, and assist in risk analysis.
- What You Bring.
- Bachelor's degree in electrical engineering or power electrical engineering, with certification as a Thai Associate Level Electrical Engineer being advantageous.
- 5 to 8 years of experience in high voltage systems and solutions, including GIS, AIS, Power Transformer, Circuit Breaker, Disconnector, Instrument Transformer, Surge Arrester, and Substation Automation System.
- Strong communication, presentation, problem analysis, and problem-solving skills, with a good command of English (both writing and speaking).
- Proficiency in MS Office365 applications and precision measuring tools, with flexibility and willingness to participate in international projects.
- Accurate and quality management in project timelines and delivery of requirements, with the ability to handle multiple projects and work towards tight deadlines.
- Team player mindset, excellent adaptability, and openness to other cultures.
- Our Grid Technologies division enables a reliable, sustainable, and digital grid. The power grid is the backbone of the energy transition. Siemens Energy offers a leading portfolio and solutions in HVDC transmission, grid stabilization and storage, high voltage switchgears and transformers, and digital grid technology.
- Who is Siemens Energy?.
- At Siemens Energy, we are more than just an energy technology company. With ~100,000 dedicated employees in more than 90 countries, we develop the energy systems of the future, ensuring that the growing energy demand of the global community is met reliably and sustainably. The technologies created in our research departments and factories drive the energy transition and provide the base for one sixth of the world's electricity generation.
- Our global team is committed to making sustainable, reliable, and affordable energy a reality by pushing the boundaries of what is possible. We uphold a 150-year legacy of innovation that encourages our search for people who will support our focus on decarbonization, new technologies, and energy transformation.
- Find out how you can make a difference at Siemens Energy: https://www.siemens-energy.com/employeevideo.
- Our Commitment to Diversity.
- Lucky for us, we are not all the same. Through diversity, we generate power. We run on inclusion and our combined creative energy is fueled by over 130 nationalities. Siemens Energy celebrates character - no matter what ethnic background, gender, age, religion, identity, or disability. We energize society, all of society, and we do not discriminate based on our differences.
- Rewards/Benefits.
- Outstanding opportunity for personal development working in an organization covering multiple facets of the energy industry and energy transition.
- Develop technical sales skills that provides SE management exposure to your successes and accomplishments.
- Exposure to obtain coaching and mentorship from experience sales peers leading to an open feedback culture.
- Provide flexible and hybrid working arrangement!.
- Readily available learning platform to support your learning growth!.
- Jobs & Careers: https://jobs.siemens-energy.com/jobs.
ประสบการณ์:
5 ปีขึ้นไป
ทักษะ:
Project Management, Assembly, GIS, English
ประเภทงาน:
งานประจำ
เงินเดือน:
สามารถต่อรองได้
- Controlling and evaluation of project progress and report to project management (time and quality).
- Coordinate all activities of suppliers, subcontractors and customers.
- Perform quality check/inspection to ensure assembly work is completed according to requirements and quality control on project to ensure engineering work meets the required standards and specifications.
- Coordinating technical support with internal and external interface partners.
- Assisting generation of reports and performing NCC-reporting to the project management.
- Ensure corrective/preventive actions are taken.
- Organizing, compiling, submitting and controlling of technical documents.
- Risk analysis on project to follow EQS policy (Environment Quality Safety).
- What You Bring.
- Bachelor s Degree in Electrical Engineering or Power Engineering.
- Certified Associate Level Electrical Engineer (advantageous).
- 3 to 5 years of experience in high voltage systems and solutions i.e. GIS, AIS, Power Transformer, Circuit Breaker, Disconnector, Surge Arrester, Protection Relay and COMS such as SCADA.
- Good command of English, both written & spoken skills.
- Proficiency in MS Office, MS Project applications and precision measuring tools.
- Flexibility and willingness to participate a certain period of time for international projects.
- Accurate and quality management in project timeline and delivery of requirements.
- Full working rights in Thailand and ability to travel.
- Our Grid Technologies division enables a reliable, sustainable, and digital grid. The power grid is the backbone of the energy transition. Siemens Energy offers a leading portfolio and solutions in HVDC transmission, grid stabilization and storage, high voltage switchgears and transformers, and digital grid technology.
- Who is Siemens Energy?.
- At Siemens Energy, we are more than just an energy technology company. With ~100,000 dedicated employees in more than 90 countries, we develop the energy systems of the future, ensuring that the growing energy demand of the global community is met reliably and sustainably. The technologies created in our research departments and factories drive the energy transition and provide the base for one sixth of the world's electricity generation.
- Our global team is committed to making sustainable, reliable, and affordable energy a reality by pushing the boundaries of what is possible. We uphold a 150-year legacy of innovation that encourages our search for people who will support our focus on decarbonization, new technologies, and energy transformation.
- Find out how you can make a difference at Siemens Energy: https://www.siemens-energy.com/employeevideo.
- Our Commitment to Diversity.
- Lucky for us, we are not all the same. Through diversity, we generate power. We run on inclusion and our combined creative energy is fueled by over 130 nationalities. Siemens Energy celebrates character - no matter what ethnic background, gender, age, religion, identity, or disability. We energize society, all of society, and we do not discriminate based on our differences.
- Rewards/Benefits.
- Outstanding opportunity for personal development working in an organization covering multiple facets of the energy industry and energy transition.
- Develop technical sales skills that provides SE management exposure to your successes and accomplishments.
- Exposure to obtain coaching and mentorship from experience sales peers leading to an open feedback culture.
- Provide flexible and hybrid working arrangement!.
- Readily available learning platform to support your learning growth!.
- Jobs & Careers: https://jobs.siemens-energy.com/jobs.
ทักษะ:
Assembly, Compliance, GMP
ประเภทงาน:
งานประจำ
เงินเดือน:
สามารถต่อรองได้
- Manage all activities related to end to end production (Mixing, Filling & Assembly).
- Responsible and accountable for related KPI s (e.g.: Safety, Quality, Productivity, Material-loss, OEE in production processes, Conversion-cost, etc.).
- Responsible and accountable for all related cost-centers.
- Drives and implements continuous improvement and cost-saving activities.
- Constantly improves working environment (ergonomics, hygiene, quality, safety).
- Plan the use of human resources. Organize recruitment and placement of required staff. Establish organizational structures.
- Delegate tasks and accountabilities, establish work schedules, supervise staff, Monitor and evaluate performance.
- Liaison with plant manager. Assist in the development of strategic plans for operational activity. Implement and manage operational plans.
- Forecast requirements, prepare investment plan, prepare an annual budget, schedule expenditures, analyze variances, initiating corrective actions which related to production activities.
- Perform other duties as assigned by superior Compliance the regulations and standard of the company (e.g., GMP, ISO 50001, ISO45001, ISO22716, etc.).
- What makes you a good fit.
- Contribute to continuous improvement.
- Ensuring cost reduction.
- Overseeing quality management.
- Experienced in Lean manufacturing and engineering manufacturing.
- Experienced in systems production.
- Some perks of joining Henkel.
- Globally wellbeing standards with health and preventive care programs.
- Gender-neutral parental leave for a minimum of 8 weeks.
- Employee Share Plan with voluntary investment and Henkel matching shares.
- Medical Coverage for employees and eligible dependents.
- Provident Fund.
- Annual Physical Examination for employees.
- Discounts on company products.
- At Henkel, we come from a broad range of backgrounds, perspectives, and life experiences. We believe the uniqueness of all our employees is the power in us. Become part of the team and bring your uniqueness to us! We welcome all applications across different genders, origins, cultures, religions, sexual orientations, disabilities, and generations.
ทักษะ:
Assembly, Mechanical Engineering, AutoCAD
ประเภทงาน:
งานประจำ
เงินเดือน:
สามารถต่อรองได้
- Conduct Gemba walks to analyze and address stamping and body assembly quality issues using problem-solving methods and quality control (QC) tools.
- Ensure accuracy in body dimensions and production processes for new model development.
- Interpret and create 3D drawings to facilitate design changes and improvements.
- Enhance production processes to boost efficiency and quality in body assembly.
- Investigate defects and implement solutions to achieve quality targets (DPHU).
- Collaborate with cross-functional teams (CFT) with R&D, production, and automotive suppliers to meet project objectives.
- Track data and report key quality information and findings to cross-functional teams (CFT) and management.
- Provide technical support to the production team to maintain high standards in body assembly.
- Engage in continuous improvement (Kaizen) activities for body assembly.
- Adhere to safety, quality, and environmental regulations in all tasks.
- Qualifications: Bachelor's degree in Mechanical Engineering, Mechatronic Engineering, Automotive Engineering, or a related field.
- Strong problem-solving skills with experience in using QC tools.
- QC Tools Knowledge: Familiarity with QC tools such as Fishbone diagrams, Pareto charts, 5 Whys, Fault Tree Analysis (FTA), root cause analysis.
- Proficient in reading and creating 3D drawings using AutoCAD, CATIA, or similar software.
- Skilled in Microsoft Excel for data analysis and PowerPoint for presentations.
- Able to communicate, discuss, and present in English (TOEIC score of 550 or higher).
- Strong leadership and decision-making skills to support the team when needed.
- Strong collaboration / teamwork skills and the ability to work effectively with various departments.
- Logical thinking, analytical skills, problem solving skills & decision making, proactive approach to challenges and learn new things.
- If you are interested in this job role, please prepare your updated resume or LinkedIn profile for the application process through the Nissan Job Portal.
- Only shortlisted candidate will be contacted for an interview".
- For more information about Nissan's products, services, and commitment to sustainable mobility, visit nissan-global.com. You can also follow us on Facebook, Instagram, X and LinkedIn and see all our latest videos on YouTube.
- Why Nissan?.
- You will definitely get the right answers why you should join us through watching the video on YouTube.
- Samut Prakan Thailand
ประสบการณ์:
5 ปีขึ้นไป
ทักษะ:
Project Management, Product Design, Compliance, English
ประเภทงาน:
งานประจำ
เงินเดือน:
สามารถต่อรองได้
- Design and develop the functional testers, including hardware & software elements, following the customer test specification/test requirement.
- Review equipment data sheets and select appropriate equipment based on requirements.
- Support creation of structural or functional test strategy and test plan to meet project goals and requirements.
- Support creation of technical proposals with costed BOM and hours estimates.
- Debug tester issues using the design of experiments, tools, and failure analysis methodologies.
- Ensure to deliver the goods and follow the project plan. Project management and cost planning.
- Provide high-level test hardware and software solution architecture.
- Provide technical support to the production team. For engineering change, fixing the fault failure issue.
- Review the tester concept design with the mechanical engineer and provide good feedback to meet the project goals and requirements.
- Collaborate with product design teams with feedback from product testability, test coverage, diagnosability, reparability, firmware/diagnostics, and user experience.
- Create reports and documentation.
- Perform tester commissioning on local / overseas.
- Drive problem-solving and corrective action related to the causes of the project issue.
- Able to support production work abroad at different times. In a necessary situation Whether it's remote control or answering emails.
- Responsible for overseeing project execution and ensuring timely completion by analyzing project scope and defining specifications.
- Develop test methods for product investigations, assess the adequacy and sequence of test programs, and examine samples to ensure compliance with requirements.
- Identify key factors [Risk/Mitigation plan ] for tester improvement and customer satisfaction enhancement.
- Prepare comprehensive reports documenting project proposals and outcomes estimation.
- Knowledge/Skills/Competencies.
- Bachelor s degree in Electronics, Industrial, Mechatronic engineering, or in a related field.
- Proficiency in developing programming languages such as Labview, Teststand, PLC, Python, Robot Framework, C and C++.
- Ability to read hardware schematic. Compare and understand equipment specifications. [Proficiency with Altium software/Easyeda is preferred.].
- Strong skill in wiring and equipment assembly.
- Have background experience in 3D/CAD review (SolidWork).
- Ability to work under pressure and with limited time, positive attitude, teamwork, and good interpersonal skills.
- Able to travel locally / overseas for test product implementation, and commissioning.
- Professional written and verbal communication skills in English.
- Males must be exempt from military service.
- Minimum of 5 years of working experience in test development or related industry.
- Strong analytical skills in innovative approaches to electrical circuit systems/PCB design development.
- Typical Experience.
- Minimum of 5 years of working experience in test development or related industry.
- Typical Education.
- Bachelor degree or consideration of an equivalent combination of education and experience.
- Educational Requirements may vary by Geography.
- Notes.
- This job description is not intended to be an exhaustive list of all duties and responsibilities of the position. Employees are held accountable for all duties of the job. Job duties and the % of time identified for any function are subject to change at any time.
- Celestica is an equal opportunity employer. All qualified applicants will receive consideration for employment and will not be discriminated against on any protected status (including race, religion, national origin, gender, sexual orientation, age, marital status, veteran or disability status or other characteristics protected by law).
- At Celestica we are committed to fostering an inclusive, accessible environment, where all employees and customers feel valued, respected and supported. Special arrangements can be made for candidates who need it throughout the hiring process. Please indicate your needs and we will work with you to meet them.
- Celestica (NYSE, TSX: CLS) enables the world s best brands. Through our recognized customer-centric approach, we partner with leading companies in Aerospace and Defense, Communications, Enterprise, HealthTech, Industrial, Capital Equipment and Energy to deliver solutions for their most complex challenges. As a leader in design, manufacturing, hardware platform and supply chain solutions, Celestica brings global expertise and insight at every stage of product development - from drawing board to full-scale production and after-market services for products from advanced medical devices, to highly engineered aviation systems, to next-generation hardware platform solutions for the Cloud. Headquartered in Toronto, with talented teams spanning 40+ locations in 13 countries across the Americas, Europe and Asia, we imagine, develop and deliver a better future with our customers.
- Celestica would like to thank all applicants, however, only qualified applicants will be contacted.
- Celestica does not accept unsolicited resumes from recruitment agencies or fee based recruitment services.
ประสบการณ์:
3 ปีขึ้นไป
ทักษะ:
Automation, Product Development, CAD, English
ประเภทงาน:
งานประจำ
เงินเดือน:
สามารถต่อรองได้
- Assist the engineering staff in studying, proposing different project feasibility concept solutions for automation projects and design of electrical systems, in terms of costs, technical feasibility, lead time, simplicity, and standardization by involving all relevant stakeholders.
- Coordinate with internal resources to ensure flawless execution of projects.
- Participate and coordinate with production in all company's activities in order to improve machines quality, productivity and meet the customer satisfaction.
- Follow the product and propose requested changes and corrections throughout the warranty period for new equipment.
- Perform risk evaluation to minimize project risks.
- Develop and evaluate experimental plans for validation of prototypes or machine improvements in relation with other departments (Continuous Improvement, Quality, Product Certification, Production).
- Work with the Engineering team for producing/updating all necessary 3D models, 2D drawing, calculation note, operation manuals and Bill of Material in accordance with applicable standards and procedures.
- Support the Continuous Improvement team when opportunities arise in automation and electrical system improvements of exist machine.
- Summarize results and conclusions in design reports, machine manuals (maintenance and operation).
- Support technical sourcing wherever applicable.
- Qualification Requirements: Bachelor or Master Degree in Mechatronics Engineering or related field.
- Min. 1-3 years of technical experience or product development in Machine manufacturing industry.
- Experience on whole machine developing or manufacturing is mandatory.
- Experience on lean product development is a plus.
- Experience on prototyping and validation is a plus.
- Experience on Mechanical and Hydraulic system is a plus.
- Experience on IIOT system is a plus.
- Experience on Solidworks Electrical Pro. is a plus.
- Experience on Schneider PLC & HMI programing is a plus.
- Good communication in English.
- Strong experience in CAD software and SolidWorks program is essential.
- Be able to create 3D models and 2D part drawing as well as assembly drawing using interlink function of Solid works.
- Good Knowledge of machinery design and problem analysis.
- Good knowledge of various international standard relating to machine design.
- Good knowledge of machine fabrication method.
- Self-initiative, enthusiasm.
ทักษะ:
Project Management, Financial Reporting, Accounting
ประเภทงาน:
งานประจำ
เงินเดือน:
สามารถต่อรองได้
- Responsible for understanding and implementing the customers technical roadmap and related process development projects.
- Lead and implement the development and release of the full manufacturing process for new customer products.
- Understand and provide feedback on customers technical requirements to team members and management.
- Responsible for developing and implementing costed and optimized feedback using Design for manufacturability (DFX) tools and processes, with the goal of reducing manufacturing cost and improving quality and reliability of product.
- Develop, plan and lead the assessment of the capability of process applications using Design of Experiments.
- Devise process controls and data collection strategies and evaluate complex data to assist with reporting yield, reliability and diagnoses to root causes failures impacting product quality.
- Ensure accurate and timely communication to management on critical technical and business issues.
- Set yearly plans and goals for the department and give direction on expected performance and provide regular performance evaluations and ongoing feedback. Accountable for all department objectives and achieving agreed targets for key performance indicators.
- Knowledge/Skills/Competencies.
- Project Management - Ability to manage/lead complex, multiple line engineering projects that may also involve other functions. Demonstrate solid understanding of the technical, financial and people aspects of the project. Able to create a project/change management plan and ensure that the project is delivered within the assigned time and budget. Ability to recognize project barriers and develop mitigation plans.
- Leadership - Demonstrate "People & Team Leadership Behaviors" as per Celestica Leadership Imperatives.
- Financial Acumen / Business Planning - Ability to create financial plans for your projects, align them internally with your line of management and other functions and externally if needed. Create project plans, profitability calculations, risk and sensitivity analysis, able to recognize barriers and mitigate profitability risks. Fully knowledgeable about internal and external financial reporting, accounting and tax requirements relevant to your area of expertise.
- The following competencies may also be required: Coaching/Mentoring; Communication/Negotiation/Presentation; Creative Problem Solving; Customer Interaction/Stakeholder Management; Quality & Lean; Working Effectively with Others; D/PFMEA; 8D/Corrective Action; Equipment Safety; Design of Experiments (DOE).
- Typical Experience.
- 10+ years of work experience in PCB assembly manufacturing field.
- Typical Education.
- Degree or higher in Mechanical/Chemical/Electrical Engineering or equivalent.
- Notes.
- This job description is not intended to be an exhaustive list of all duties and responsibilities of the position. Employees are held accountable for all duties of the job. Job duties and the % of time identified for any function are subject to change at any time.
- Celestica is an equal opportunity employer. All qualified applicants will receive consideration for employment and will not be discriminated against on any protected status (including race, religion, national origin, gender, sexual orientation, age, marital status, veteran or disability status or other characteristics protected by law).
- At Celestica we are committed to fostering an inclusive, accessible environment, where all employees and customers feel valued, respected and supported. Special arrangements can be made for candidates who need it throughout the hiring process. Please indicate your needs and we will work with you to meet them.
- Celestica (NYSE, TSX: CLS) enables the world s best brands. Through our recognized customer-centric approach, we partner with leading companies in Aerospace and Defense, Communications, Enterprise, HealthTech, Industrial, Capital Equipment and Energy to deliver solutions for their most complex challenges. As a leader in design, manufacturing, hardware platform and supply chain solutions, Celestica brings global expertise and insight at every stage of product development - from drawing board to full-scale production and after-market services for products from advanced medical devices, to highly engineered aviation systems, to next-generation hardware platform solutions for the Cloud. Headquartered in Toronto, with talented teams spanning 40+ locations in 13 countries across the Americas, Europe and Asia, we imagine, develop and deliver a better future with our customers.
- Celestica would like to thank all applicants, however, only qualified applicants will be contacted.
- Celestica does not accept unsolicited resumes from recruitment agencies or fee based recruitment services.
ประสบการณ์:
5 ปีขึ้นไป
ทักษะ:
Project Management, Compliance, Product Design
ประเภทงาน:
งานประจำ
เงินเดือน:
สามารถต่อรองได้
- Lead and mentor the engineering and product performance teams in their assignments, fostering a collaborative and productive work environment.
- Coordinate activities with other functions and departments, ensuring seamless integration and communication across the organization.
- Set project priorities based on their strategic importance to the Group, ensuring alignment with overall business goals.
- Organize and participate in knowledge transfer within Dextra Group, promoting continuous learning and development.
- Prepare and present weekly and monthly reports, including detailed time management and risk analysis, to keep stakeholders informed and projects on track.
- Propose and implement in coordination with HR the learning path of direct subordinates consistently with Dextra's needs (Individual Development Plans).
- Implement the HR Policies and the company PMS process (set up KPls and competencies, regular feedback and 1/1, final assessment, career path proposition).
- Keeps management informed about progress and problems, mitigate risks, and propose action plan.
- Contribute to the Company Dashboards elaboration and filing.
- Design Engineering: Implement and oversee project management systems to ensure a systematic approach to all engineering projects.
- Manage and coordinate engineering changes within the company, ensuring smooth transitions, compliance with standard and quality requirements and minimal disruptions.
- Lead and facilitate development projects through design, transition, and industrialization stages, ensuring timely and successful completion.
- Conduct and supervise engineering calculations, product simulations and assessments through Finite Element Analysis (FEA) and studies on products, ensuring accuracy, reliability and provide expert guidance.
- Develop and present recommendations and proposals related to product design and manufacturing, based on thorough calculations and simulations.
- Establish guidelines and instructions for common product calculation methods, ensuring consistency and best practices.
- Coordinate and manage subcontracted studies with outside agencies, ensuring alignment with company standards and objectives.
- Perform and oversee risk management activities to minimize project risks and ensure project success.
- Product Performance Oversee the investigation of product issues, utilizing root-cause analysis methods, and communicate findings, advice, and solutions to sales staff, customers, and regulatory agencies.
- Prepare detailed reports on sample preparation and investigations, including root cause analysis.
- Provide on-site and remote support to Dextra customers on product certification projects, offering instructions and consultations in coordination with the Product Certification team.
- Coordinate and lead the assignment of Engineers in assisting the preparation of splice samples both locally and abroad.
- Ensure compliance statements in commercial documentation are accurate and up-to-date.
- Coordinate the preparation and control of technical documentation (Datasheets, Assembly instructions) with other functions.
- Develop and document standard solutions and methods for frequently raised issues in a FAQ system for various product ranges.
- Supervise and coordinate the team s participation in academic research programs whenever applicable.
- Provide recommendations and proposals for product design or manufacturing based on research and experimental testing as a result from product performance investigations.
- Support in the validation of construction methods trials in our workshop when required.
- You may also be assigned additional duties as needed. On the scope of work described above, produce weekly and monthly reports to your manager to track the project advancements (actual vs forecast) including root cause analysis.
- Functional Competencies.
- Project management: Manage project execution to ensure adherence to budget, schedule and scope including execution and communication with project team and steering committee.
- Continuous improvement: Define or modify product / equipment or processes to improve performances (resource or cost efficiency ).
- Process analysis: Analyze operational, process, production, economic or other data to understand and capitalize on process characteristic and limitation to provide conclusion/solution.
- Product applications understanding: To analyze customer needs, challenges and technical construction applications, to drive Dextra's offer to meet those expectations in an impacting manner. Product Knowledge.
- Engineering and technical knowledge: To interpret and produce engineering drawing (mechanical, electrical,&hellip.).
- Computer skills: To use Outlook, Word, PowerPoint, Excel, intranet, internet, ERP (as applicable) at the level needed for the work application.
- General Competencies.
- Customer orientation.
- Can do attitude.
- Pro-active personality.
- Analytical thinking.
- Building collaborative relationships.
- Communication information.
- Information gathering.
- Organizational awareness.
- Planning and organizing.
- Listening and understanding.
- Managing change.
- Written communication.
- Time management.
- Qualifications Bachelor s or master s degree in mechanical engineering, civil engineering, or other related Engineering disciplines.
- 5+ years of relevant experience in design engineering or civil engineering, with experience in project management.
- Experience working in similar management role, leading technical teams toward successful product delivery.
- Excellent written and verbal communication skill.
- CAD application.
- Solidworks/ Solidworks PDM.
- Microsoft Office.
- Project Management Software.
- Strong creative thinking and problem solving.
- Self-initiative.
- 1